Electrical Overhaul
One of the major projects Mark has successfully tackled on the new boat was a complete electrical overhaul of the main DC power distribution. There is plenty of room around the newly installed, compact lithium battery bank in which to work⦠make that enough room!
Weβd been noticing among other projects like the head installations that the boat is underwired. More than likely, when the Dolphin was built in Brazil it was specβd for 220V AC, 24V DC infrastructure, yet outfitted with 110V AC and 12V DC electrics.
Mark found this wire melting in a conduit when he recently replaced the fresh water pump and wires, something we were using frequently! All factors have been pointing to the need for our electrical overhaul.
It all started when our new Victron 3000W inverter/charger arrived. This replaced the existing Mastervolt 2500W inverter/charger, primarily because we are used to the programmability of the Victron to manage our LiFePO4 battery banks. Specifically, we manage bulk voltage, absorption, float parameters for charging and low voltage cutoff & reconnect for inverting and battery management.
The result was a clean install of the inverter/charger, mounting it in a new location, shortening runs while replacing all DC and AC wires and fixing the safety ground⦠these photos are of the work in progress ~ I forgot to take a photo of the final install before we filled the space back up with tools & parts.
Moving on to the main DC distribution system, the existing main fuses were replaced at the battery bank. There were three 250A fuses of industrial quality, yet bulky in a big fuse-holder box with unclear replacement sources. The 250A fuse was underrated for the inverter/charger so we increased two of the three fuses to 400A.
Importantly, a cutoff switch was added to the battery bank as well as a shunt for the battery monitor. In addition, there are sensor wires added to the bank for the battery monitor power, inverter/charger, solar and soon to come, the alternators. In the plastic tube are run sensing wires for the cell log to monitor state of charge for the 3P4S LiFePO4 cells.
Mark shined up the copper bus bars with Deoxit & 400 grit emery and upsized all wiring leading to and from the batteries. In general, we used 4/0, 2/0, 2AWG and 1AWG wires for the main distribution. Some existing 4/0 wire could be reused and we took it over to Best Boat Wire to have them cut and add terminals. After years of using them on the internet (also known as Genuine Dealz), we were excited to find them right down the street from the marina in Brunswick!
After noodling it for some time, Mark wired up the main DC system in short order, adding appropriate main breakers. He drew up a schematic of the system to help me visualize it and and I whipped up this pictorial to have handy.
As an example of re-wiring, the wire from the battery bank (bus bar) to the house panel was upsized from 6AWG to 2AWG. The House panel itself and wiring conduits are in the process of being optimized with branching circuits, etc!
Another upgrade in the making for us was the primary electric winch. We were spoiled by the speed of the winch on the Manta for fast and easy mainsail raising, and couldnβt believe how slow the existing winch was in raising the sail. Granted, the Dolphin has a much bigger sail and requires a 2:1 purchase on the main halyard, making it inherently 1/2 as fast as a single purchase.
Still, we appreciate the efficiency of fast sail work without the need for tons of sea room to work with, so decided to upgrade the winch from an Antal 48 to a Harken 46. The difference in speed is just over 2x, going from 12.5 m/min to 26.7 m/min.
The hole left in the deck from the former winch was bigger than it needed to be for the Harken. In addition, the bolt pattern was different, so extra holes were filled with epoxy putty.
Since the bottom of the winch is built to drain water through a few recesses and channels, we had to figure out how to stop water from draining into the boat. The option given by Harken was to fill the bottom of the winch base with caulk, but that would inhibit regular drainage as well. Mark fashioned up a fiberglass plate to go under the base of the winch, where he could then seal the inner hole with sealant while still letting water drain out of the winch base but not into the boat.
The installation required some boat yoga to hook up the 30 lb motor under the cabin top, upside down and backwards! The motor also required an increase in wiring (1AWG) to the new solenoid control box, now fused with an 80A breaker from the mains.




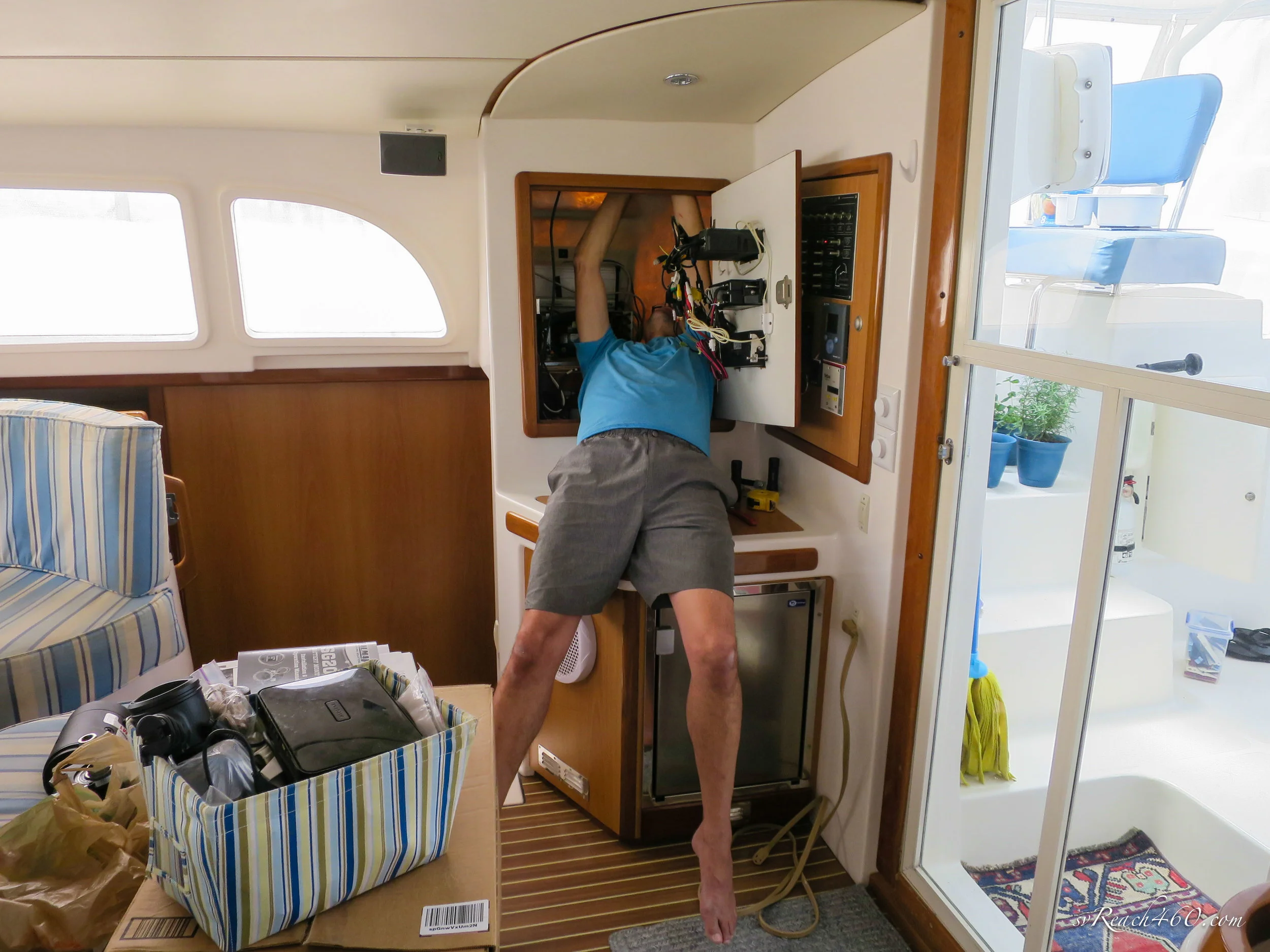



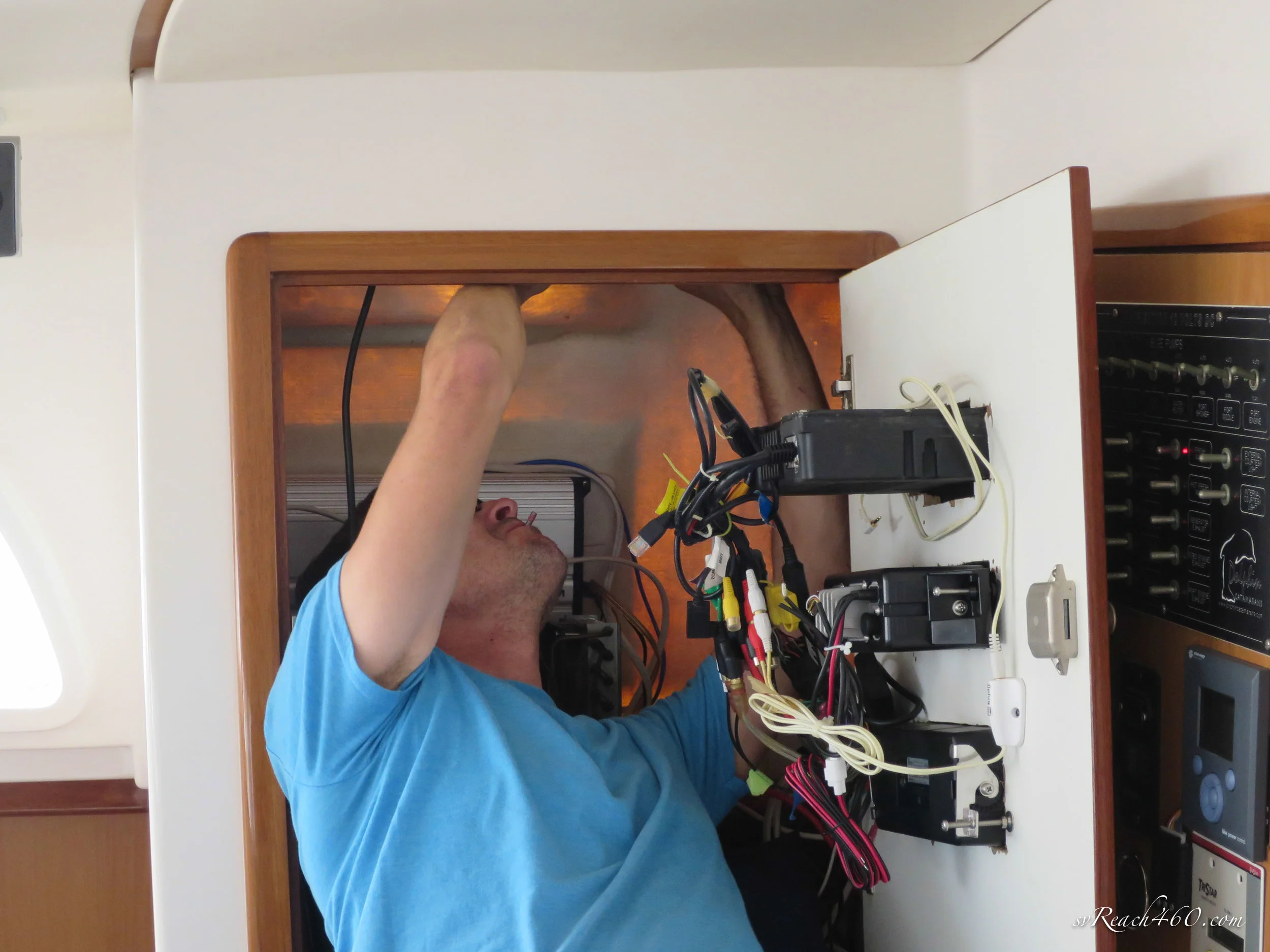


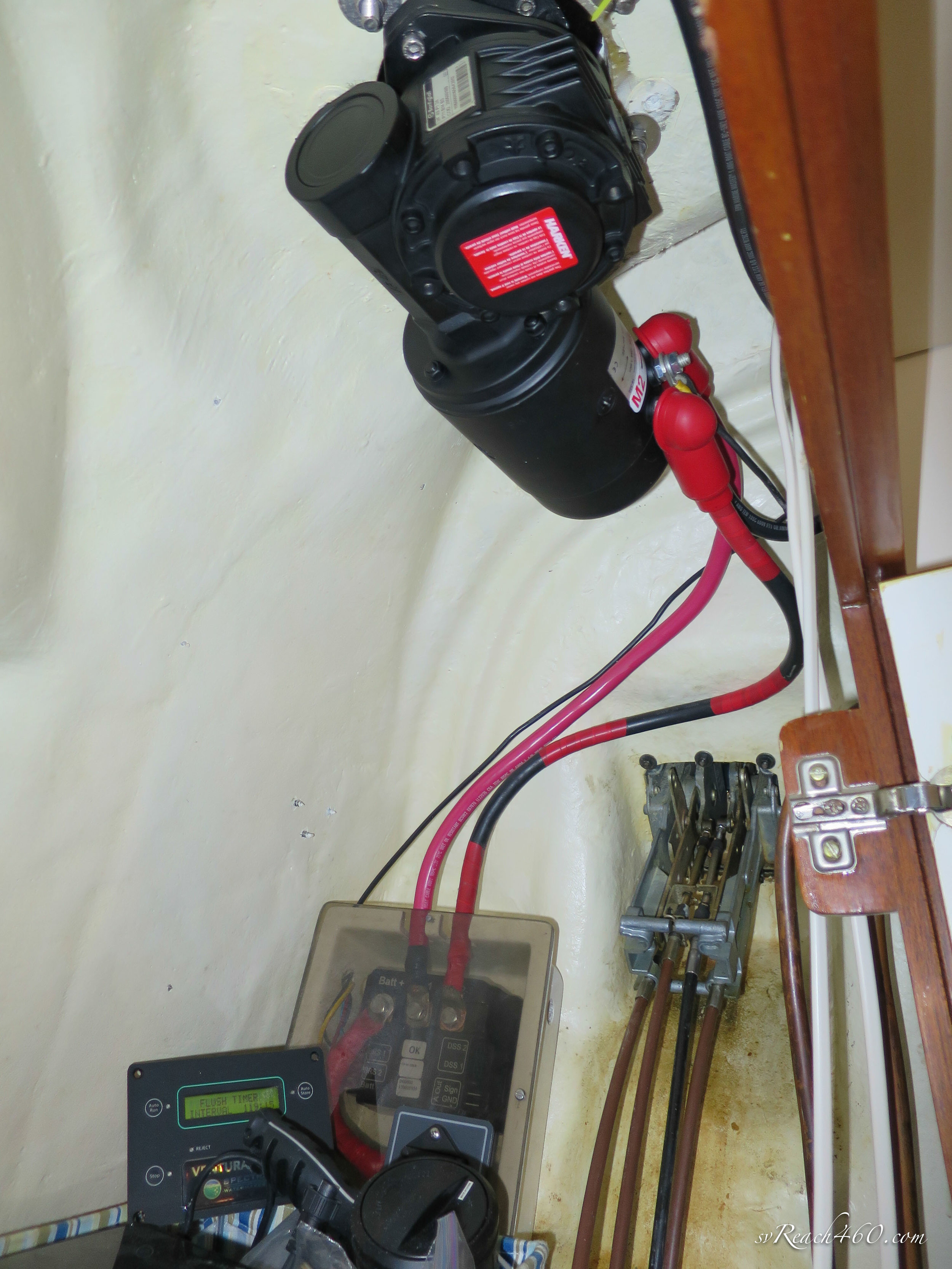
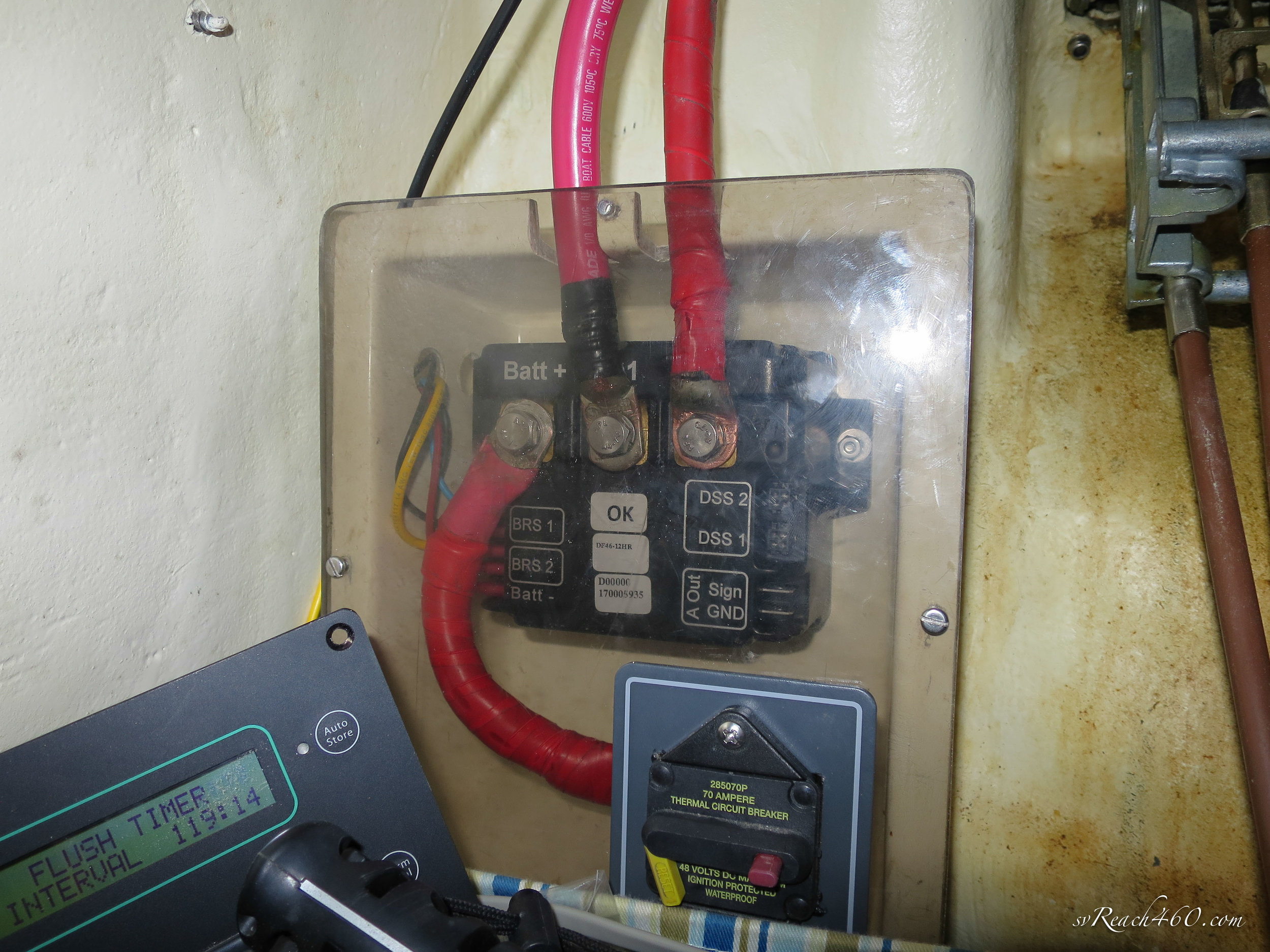



We tested the new winch on a calm day. It works very well and much faster, as advertised. Seeing the sail raised made me wish it was time to sail away, but not just yet. Hurricane season is approaching and there are a few more major projects left on the list!